Электрополировка стали для насосного оборудования – распространенная технология, применение которой позволяет обеспечить соответствие перекачивающих агрегатов строгим гигиеническим требованиям к оборудованию для ряда производственных процессов. Как правило, речь идет о насосных аппаратах для пищевой, косметологической, фармацевтической и ряда иных производств, где недопустимы застои либо отложения на внутренней поверхности гидронасосов.
Электрохимическая полировка металла призвана оптимизировать гладкость, чистоту, химическую пассивность, отражающую способность поверхности либо сочетания нескольких этих показателей. Но основная цель процесса – обеспечить заданную величину шероховатости поверхности изделия.
Сама процедура заключается в электрохимическом воздействии на изделие либо заготовку из нержавеющей либо иной стали, при котором с ее внешней поверхности удаляется тончайший слой металла. В итоге обрабатываемая поверхность приобретает гладкость, чистоту и блестящий облик. При этом на поверхности образуется особая пленка (оксидная либо гидроксидная), которая обеспечивает указанные свойства.
Если рассматривать саму технологию обработки, то электрохимическая полировка металла фактически представляет собой обратный гальваническому покрытию процесс. Электрический ток служит для удаления слоя ионов металла в растворе электролита. Это происходит в растворе электролита под воздействием тока на анод, которым служит изделие, и катод, представляющий собой инертный металл. На финальной стадии процессе компоненты процесса пассивируются в азотной кислоте, закрепляющей химическую нейтральность верхнего слоя нержавейки.
Электрохимическая полировка металла призвана оптимизировать гладкость, чистоту, химическую пассивность, отражающую способность поверхности либо сочетания нескольких этих показателей. Но основная цель процесса – обеспечить заданную величину шероховатости поверхности изделия.
Сама процедура заключается в электрохимическом воздействии на изделие либо заготовку из нержавеющей либо иной стали, при котором с ее внешней поверхности удаляется тончайший слой металла. В итоге обрабатываемая поверхность приобретает гладкость, чистоту и блестящий облик. При этом на поверхности образуется особая пленка (оксидная либо гидроксидная), которая обеспечивает указанные свойства.
Если рассматривать саму технологию обработки, то электрохимическая полировка металла фактически представляет собой обратный гальваническому покрытию процесс. Электрический ток служит для удаления слоя ионов металла в растворе электролита. Это происходит в растворе электролита под воздействием тока на анод, которым служит изделие, и катод, представляющий собой инертный металл. На финальной стадии процессе компоненты процесса пассивируются в азотной кислоте, закрепляющей химическую нейтральность верхнего слоя нержавейки.
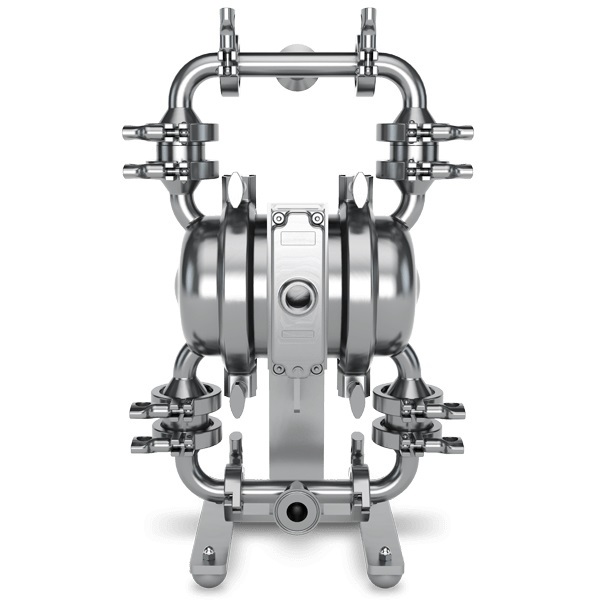
Стоит отметить, что электрополировка металла представляет собой микропроцесс. То есть она не заменяет шлифование, уплотнение пескоструйной обработкой и механическую полировку, а только служит их дополнением.
Преимущества и недостатки электрополировки стали
Сильные стороны применения этой технологии для насосного оборудования включают следующие пункты:
Несмотря на множество перечисленных достоинств, метод обработки внутренней поверхности гидронасосов из нержавеющей стали не является идеальным. Ему присущи и некоторые недостатки:
- Повышение прочности стали за счет удаления напряженного либо деформированного слоя металла;
- Повышение срока службы. За счет исключения коррозионных процессов на поверхности детали благодаря образованию защитного слоя повышается ресурс изделия;
- Отсутствие скрытых дефектов, ослабляющих структуру изделия;
- Повышение герметичности емкостей, подвергаемых такой обработке;
- Высокая скорость протекания процессов;
- Высокая эффективность в сравнении с процедурой пассивации;
- Возможность реализации в отношении широкого спектра сплавов;
- Возможность работы с большими по размерам изделиям (в том числе, сложной формы).
Несмотря на множество перечисленных достоинств, метод обработки внутренней поверхности гидронасосов из нержавеющей стали не является идеальным. Ему присущи и некоторые недостатки:
- Сложность технологии. Для обработки детали из различных сплавов необходимо приготовление индивидуального раствора с конкретными пропорциями компонентов электролита. Кроме того, величина подаваемого тока также варьируется и подбирается под конкретную задачу;
- Высокий расход электроэнергии. Технология является довольно энергозатратной, что сказывается на конечной стоимости оборудования, которое подвергнуто подобному процессу;
- Невозможность ликвидировать значительные дефекты – трещины и впадины больших размеров.
Ассортимент насосов с электрохимической полировкой
В каталоге компании «АрмапромТехно» представлен широкий ассортимент насосов различного типа (в основном, мембранные), изготовленные с применением электрополировки. В частности, к таковым относятся модели следующих брендов:
Эти и другие модели насосного оборудования, отличающиеся в результате процедуры электрополировки массой перечисленных достоинств, можно заказать у нас на выгодных условиях. Менеджеры компании готовы ответить на любые возникшие вопросы. Оставьте заявку на консультацию любых удобным вам способом – и вы получите всю необходимую информацию для принятия решения по выбору того либо иного агрегата для нужд вашего предприятия.
- Verderair: HCP15 FD, HCP25 FD, HCP50 FD, HI-CLEAN VA-H20 FD, HI-CLEAN VA-EH50 FD и другие;
- Graco: SaniForce 1040, SaniForce 2150, SaniForce 1590 HS, Husky 716 и так далее;
- Tapflo: CTH, CTX H, CTS;
- HOMMAK: S-HM5, высоконапорные Y-HM200 и другие модели гидронасосов;
- Tecnicapompe: TS, TCN, TEH, TSM;
- Yamada: NDP-5;
- Netzsch: NEMO SH PLUS, NEMO Mini BH, NEMO BH, NEMO SA;
- ARO: PD10A, PD20A, PD30A.
Эти и другие модели насосного оборудования, отличающиеся в результате процедуры электрополировки массой перечисленных достоинств, можно заказать у нас на выгодных условиях. Менеджеры компании готовы ответить на любые возникшие вопросы. Оставьте заявку на консультацию любых удобным вам способом – и вы получите всю необходимую информацию для принятия решения по выбору того либо иного агрегата для нужд вашего предприятия.